Among alternative traditional vibratos, in addition to Bigsbys and Gibsons,
there are at least four more types that are still adopted on reissues and renditions of vintage guitars:
- the Fender Floating Tremelo or
Tremolo, patented in 1961 and installed on Jazzmaster and
Jaguar guitars. It has one spring, a knife edge base plate and is lockable
via a knob. Operation is fair if used with delicacy
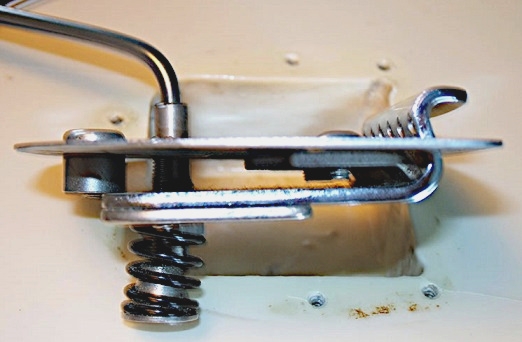
- The Fender Dynamic Vibrator,
with two springs, mounted on the Mustang (1964). As the Floating Tremolo, it
works in combination with the bridge
- The Mosrite Vibramute,
a fine aluminum system that includes vibrato, a bridge and a damper. The
design is close to Bigsby's one.
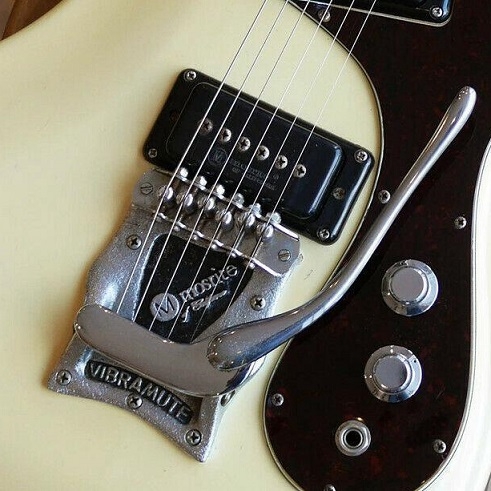
- The Epiphone Tremotone, a
bearing operated vibrato used on Epiphone guitars, and later on equipped with a
spring under the arm as the Bigsby. The company was acquired in 1957 by Gibson,
that used the Vibrola name for this Epiphone system too. The bar worked in
loosening and had different diameter seats for the strings, thus optimizing
the sound effect in the guise of a pedal steel.
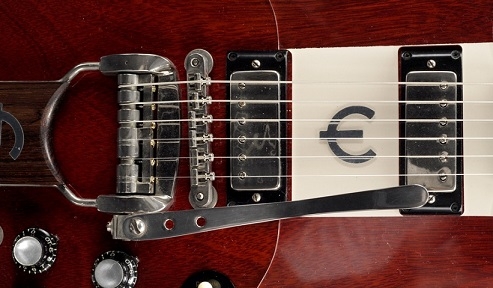
However, this article deals with three other vibratos
of greater importance, though very less popular than the classic Stratocaster
one and its floating and locking followers treated in dedicated articlesdedicated articles on the Soundsation blog. Before going on, a brief premise...
Les Paul's garage-studio in Hollywood
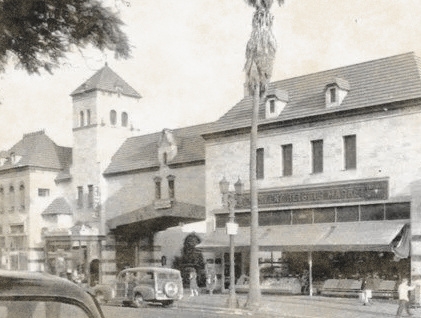
In the article “Crossed destinies of Les Paul, Leo Fender and Paul Bigsby” perhaps you read that Les Paul's place in Hollywood was
frequented by friends that were relevant for the electric guitar development:
Leo Fender and Paul Bigsby. During those evening meetings based
on beer, barbecue and good music, they shared ideas on multiple recording, tape echo, lap steels to be played with a slide, future solid-bodies and their parts.
The Kauffman Vib-Rola
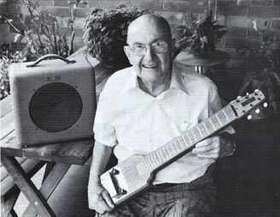
Doc Kauffman was a
friend of Les Paul too. A Rickenbacker associate, in 1928 Kauffman
applied for a patent for his Apparatus
for producing tremolo effects.
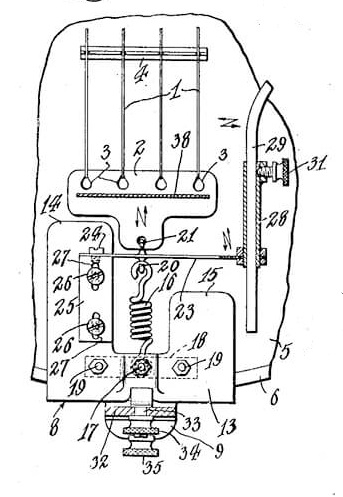
The Kauffman Vib-Rola was mounted by Les
Paul on his experimental The Log (some sources report that the
guitar player used a creation of his own), by the Gibson company on some
ES-150s, by Epiphone as an option and by Rickenbacker on some bakelite Electro
Spanishes of the '30s.
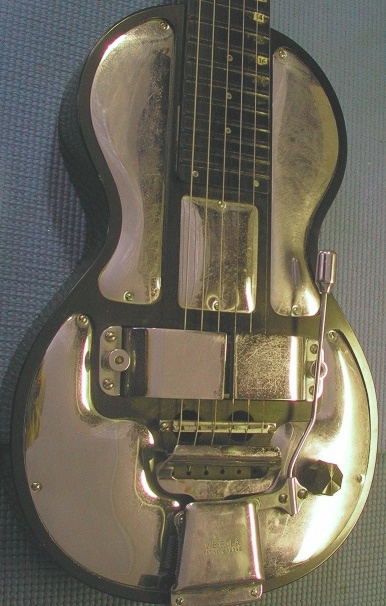
Designed to simulate a lap or pedal steel
pitch variations, the Vib-Rola was also proposed as an unfortunate motorized
version for the Vibrola Electro Spanish guitars of 1937!
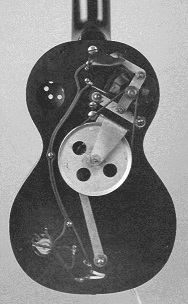
Rickenbacker continued to use the Kauffman system
until the '60s.
In the second half of the '40s, singer and guitar
player Merle Travis asked Paul Bigsby to fix the Kauffman Vib-Rola of his
Gibson L-10, thus starting a new chapter in the vibrato story (see the article
“Crossed destinies of Les Paul, Leo Fender and Paul Bigsby”).
The Kauffman vibrato arm movement was lateral
to the guitar longitudinal axis, instead of vertical. The device was formed by
a metal bracket connected to one or two springs and to the tailpiece, with a
slightly rocking bridge. The system was clever and pioneering, but had
problems in tuning retaining.
Gibson Vibrolas: the Sideways
During the '50s, besides adopting the Bigsby
vibrato under license, Gibson relied on its own Vibra-Rest, a
stylized guitar shaped device to be mounted directly over the strings between
the bridge and the trapeze tailpiece of arch-tops, taking advantage of
their related mobility.
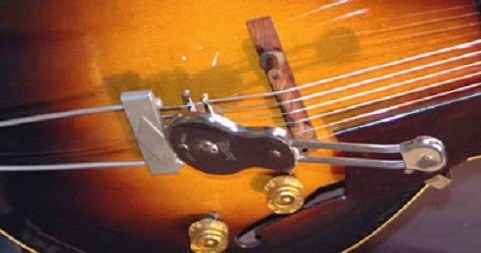
The arm of the following Sideways Vibrola
(1961-1962) operated laterally, similarly to the Kauffman, but it was based on
a heavier, more complex and solid mechanism. It was unsuccessful and was
abandoned. Today, Gibson proposes it again on reissues for accuracy reasons.
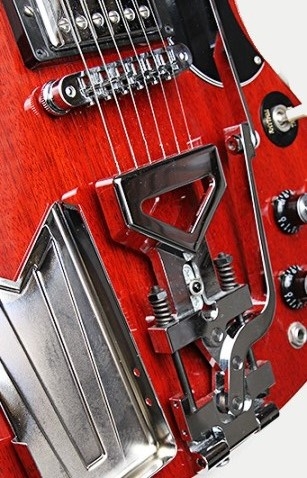
Gibson Vibrolas: the Maestro
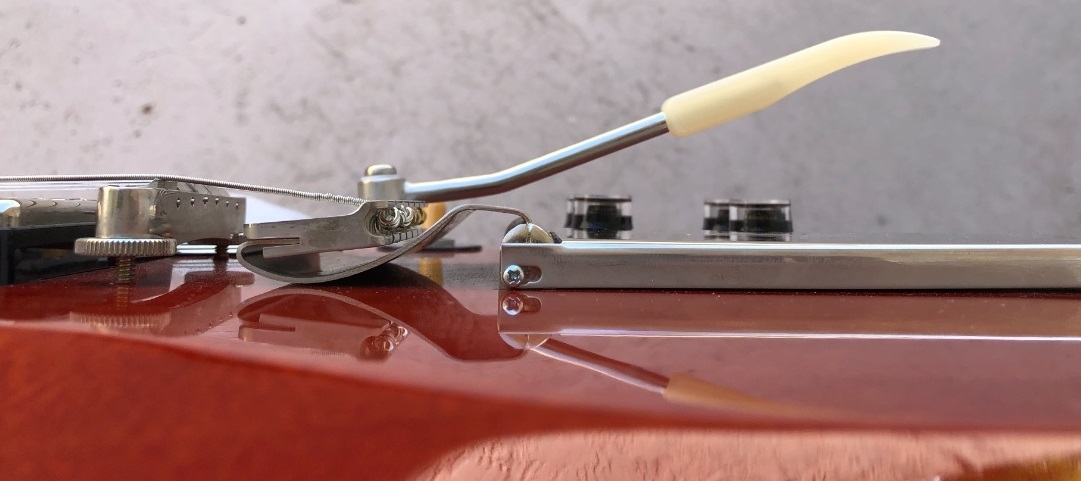
Back in the '60s Gibson solid-bodies, in particular SGs
and Firebirds, were extensively equipped with a vibrato based on the
elasticity of a bent metal sheet tangentially layed over the guitar top. Named
the Maestro Deluxe or Lyre Vibrola according to versions,
this vibrato could be long or short, with or without a lyre engraved cover,
sometimes with a mother-of-pearl inlaid ebony terminal.
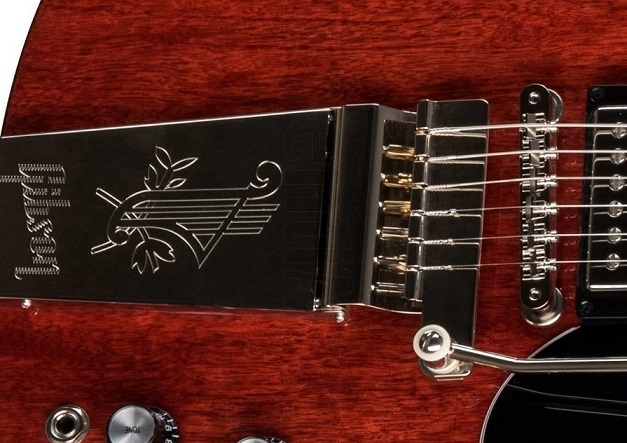
The Gibson Vibrola Setup
Except for licensed Bigsbys, it is often said of
Gibson vibratos that the best way to make them work is not to use them or even
disassemble them, as lots of guitar players actually did even on valuable and vintage
instruments.
Looking at the string angled trends on a
classic Gibson head-stock, symmetric and bent backwards, I would add that
flowing and precise operation of vibrato is never easy in this case, especially
for the third and fourth strings.
If you do want to use a Gibson Vibrola, you can
optimize its operation lubricating the nut grooves with graphite from
time to time (a soft pencil will work). Bone nuts as well as self-lubricating
ones have to be perfectly cut and polished. It is important that Tune-o-matic
bridge studs are screwed directly into the wood,
without anchors, unless they have rolling saddles (roller bridge).
That way a slight swing of the bridge is allowed, accompanying the vibrato
operation. You can see that the nut and the saddles are hindering the string
movement if you hear some rattling noise while tuning or using the arm.
To optimize tuning holding, it is important to put new
strings cleverly and to stretch the wound ones. You
can do this by bending them with your fingers, thus lightly loosening
the core to winding contact.
The Bigsby True Vibrato
The practical advises about nut lubricating and cut are also valid for the Bigsby True Vibrato,
by far much more successful than the Gibson Vibrola versions.
This system was presented in 1951 and has been
surviving through the decades until today. It is still very popular and
appreciated, thanks to a good performance if moderately used as a
colour. Among its virtues there are also the operation smoothness and
the possibility of a minimal upwards movement. As to excursion it
is no match for a floating bridge, but it keeps the tuning well and its sound
contribution is more “consistent” with hollow, semi-hollow as well as
solid-body guitars, whereas the Fender vibrato, with its routing and springs, gives a strat sound
to any instrument has been equipped with it.
Today the Bigsby brand is a property of Fender Musical
Instruments Corporation. There are US made models, with high quality and price
(Kalamazoo Series, made in aluminum), and licensed Asiatic versions
(Lightning Series, in aluminum too).
Bigsby design
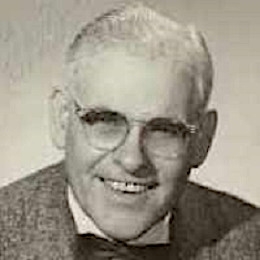
To make its vibrato, Paul Bigbsy took advantage of his experience
as a metallurgist of motorbike parts. He drew the project on paper, made a
wood model, poured the aluminum into the mold (sand-casting) and so a new piece
of guitar history was born: the Bigsby B6 vibrato! We don't know why
Paul numbered it in this way...
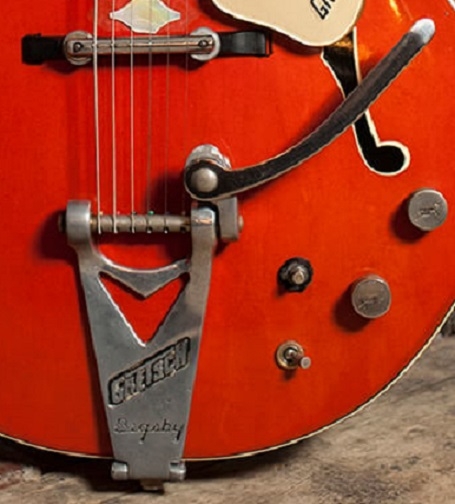
The Bigsby vibrato is based on a rocking or rocker bridge that slightly swings under the string back and forth movement when the arm is acted on. In the beginning it was suitable to hollow body guitars, it hadn't individual saddles and was conceived for the wound third string of that time. Later preset intonation or rolling saddle bridges appeared, but it is frequent to see the Bigsby vibrato paired with Tune-o-matic style bridges that are directly inserted into the wood.
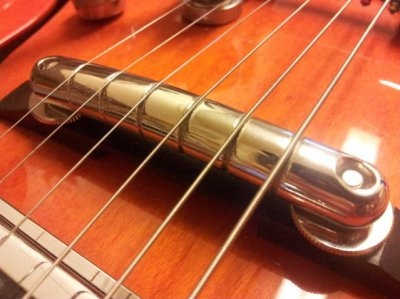
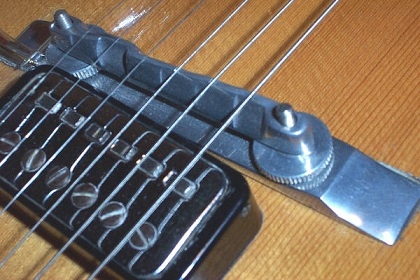
A spring
placed under the arm balances string tension. Moving up and down the arm, the
spring is compressed/loosen. Initially the strings passed under a bearing
roller that worked as a tailpiece. In the B7 model a second roller was
added to increase the string angle. This feature appeared on the solid-body
B5 model too (also called horse-shoe).
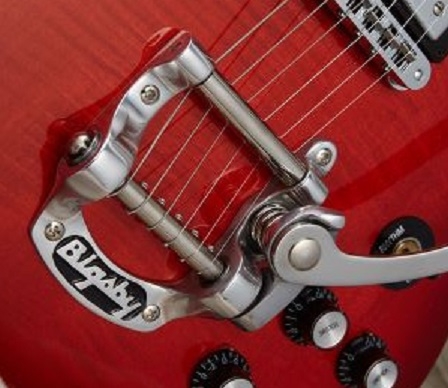
The
Bigsby vibrato has a limited action range, just a slight intonation
decrease, but it is very sensitive and soft to operate. In addition to fixed
length arms, there are some adjustable and ergonomic models, as the one
adopted on Chet Atkins dedicated Gretsches (wire arm).
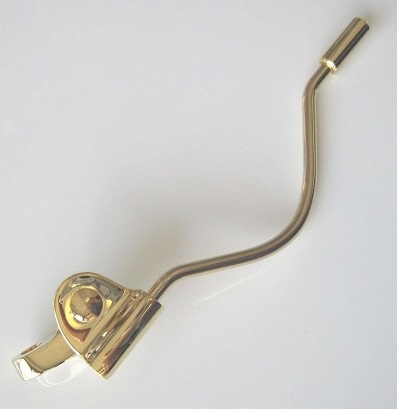
How to use a Bigsby
If it is long enough, some guitar players use the
Bigsby arm holding it in the palm of their hand. Other players hold it
under or between the little and the ring fingers. Instead, Duane Eddy's
famous effect at the beginning of the song Peter Gunn (H. Mancini, 1958)
is obtained picking the open sixth string while the left hand pushes the arm
(tune the guitar a semitone up or add a capo at the first fret).
In order not to find yourself with the arm too far ahead or backward of your
needs, it is important that the guitar is equipped with the proper
length Bigsby (short or long). It can vary from about 194
millimeters (B3) to 235 (B6). Look at the company website for models for every
kind of guitar, including Telecasters (B16).

The Bigsby setup
The Bigsby vibrato is as solid and well designed as
simple. Check that every part movement is smooth. Bearing rollers should rotate
freely. If needed, needle bearings can be cleaned from time to time with
lighter fuel and lubricated with lithium grease, but you'd better turn
to a technician for this.
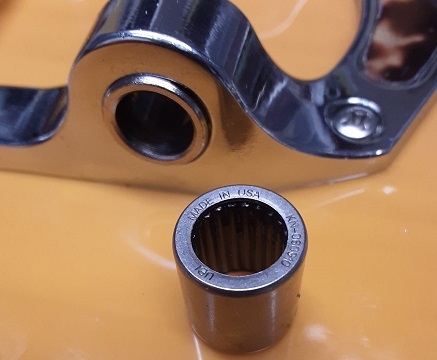
You can find alternative rollers with sealed
bearings on the market.
Before changing the strings, raise the arm and turn it
back. Check the arm bracket Allen-wrench. Adjust the arm rotation resistance
nut located under the arm.
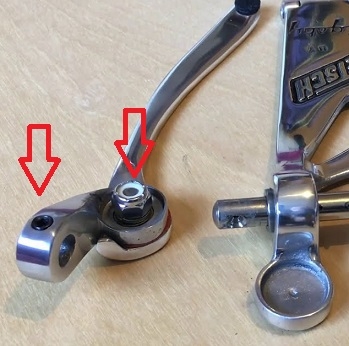
Take care not to loose the nylon seal under the
spring. It should be in perfect condition and not flattened. To get a different
feeling, you can substitute the spring with a different one available on
the market.
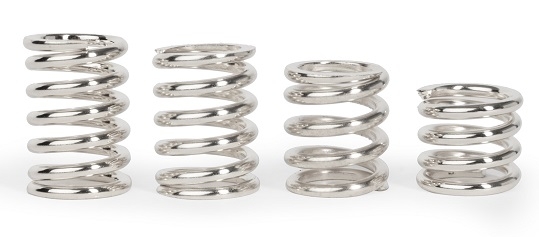
To make new string putting easier, preform the rewound
terminal (ball side) in a bent way, helping yourself with a clamp or a
cylindrical object. After the installation, remember to stretch the
strings.
If the bridge studs are inserted in anchors, it's good
the bridge to be a roller one. Verify that the strings don't touch the
bridge edge before reaching the vibrato.
As I said, lubricate the nut with specific maintenance products. This last trick is intended for the best
DIYs and for your luthier: if you notice creackings and troubles in vibrato
return to the initial tuning, check the nut trimming: strings
should be slightly accompanied towards the respective tuners.
Especially on arched top solid-bodies with a B5, check
that the vibrato body is well placed and the rollers are perfectly lined up
to the bridge. If needed, you can act on fastening screws. There are adapters
as the Vibramate that are designed for this purpose.
That's all. Enjoy your vibrato and have a
great twang!
Fabrizio Dadò